Reduce, reuse, recycle: sustainable design concepts for battery systems
September 26, 2023
A sustainable battery concept requires a variety of environmentally and climate-friendly as well as resource-saving processes, materials and applications. To be able to apply the guiding principles of the “three Rs” – Reduce, Reuse and Recycle – properly to battery concepts, it is important to consider the entire development and production chain.
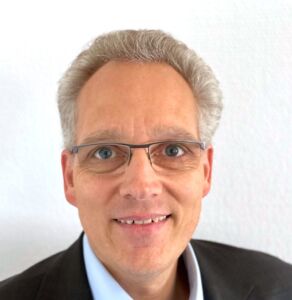
Dr. Frank Diehl, Head of Sales and Marketing, EAS Batteries and author of this article
A sustainable battery concept requires a variety of environmentally and climate-friendly as well as resource-saving processes, materials and applications. To be able to apply the guiding principles of the “three Rs” – Reduce, Reuse and Recycle – properly to battery concepts, it is important to consider the entire development and production chain.
This is already the first and fundamental chance to design sustainable battery systems, because in general hardly anyone is responsible for this entire chain.
But it is precisely this holistic view that provides an enormous potential for sustainability. The reason: the “three Rs” can be applied to the individual development and production steps of the entire chain to a greater or lesser extent, but at the same time they are mutually dependent. Those who are partially responsible for individual design steps and act with this awareness can also implement sustainable battery concepts by choosing transparent sustainable product supply or suitable raw materials.
Ultimately, it is the decision of the individual actors along the chain as well as the attitude of society as a whole that steers the path to battery technology sustainability, either through sustainably oriented demand or even through regulation. Approaches and ideas for this already exist at every level. But in concrete terms: How can the “three Rs” be applied to battery technology developments and what challenges still need to be mastered here?
The first R: Reduce
The basic idea of the guiding R “Reduce” is material efficiency. On the one hand, this refers to battery technology de-velopments in the question of how more energy can be stored per kilogram of battery. On the other hand, this mate-rial efficiency refers to the adaptation of the application. What power or function is actually needed? This application-specific development of a sustainable battery system begins at the cell level with the selection of cell chemistry. Which active materials are used and how are they produced? A positive example would be lithium iron phosphate (LFP). It does not require any rare substances and can be produced sustainably. The production method at cell level also plays a sustainable role. For example, a dry coating process for the electrodes is significantly more energy-effi-cient and environmentally friendly than the usual wet coating process. Details in the cell design that lead to a reduc-tion in the complexity of the cell also make a preparatory contribution to sustainability by creating better precondi-tions for the second and third R. One example here could be “tabless contacting”.
At the cell-pack level, too, the focus is on preparation for later reuse or recycling. The aim is to keep the number of components and different materials to a minimum. This applies to the entire bill of materials as well as to the number of components that have to be assembled. This approach reduces both costs and effort and, on the other hand, may lead to components can be disassembled more easily later for the steps of the second R and that materials can be separated from each other more easily in process of the third R.
The selection of the cells also influences the sustainability depth of the battery concept at the cell pack level. A devel-oper can implement the guiding principle “Reduce” to lower the complexity of the design much better with LFP cells than with cells based on nickel, manganese and cobalt. The reason for this is that for NMC cells he has to make a sig-nificantly higher effort and material input to guarantee the safety of the battery. LFP cells, on the other hand, offer maximum safety with less effort like integrated insulation devices, for instance. And finally, the guiding principle of reduce also implies that there is less to be consumed and less to be recycled. This certainly is a significant effect to sustainability.
The second R: Reuse
The guiding principle “Reuse” finds optimal conditions when materials, components or assemblies can be easily sepa-rated from each other and thus can directly be reused. However, to reuse entire battery units or parts of them in other contexts, further measures are required. One problem, for example, is the sealing of cell packs or modules with resin-based potting materials, which is common in the automotive industry. This process annihilates the chance of reusing individual components of the module. In most cases, potting is a commercially driven decision that could be dispensed with in favor of sustainability – as long as no safety criteria are attached to it in the individual case. To con-tinue using the entire pack, reliable information about the exact ingredients of the cells and the so-called state of health (SoH) of the battery would also be necessary. According to the EU directive, both will be provided in the future by the battery passport, but this would not be feasible for non-EU imports, for example. Another challenge is that cell technology is developing much faster than the service life of its application. The composition of materials changes almost every year, while a car battery remains in use for five to ten years. After that, it is still efficient, but no longer at the current state of the art. In addition, the material compositions of cells or packs are not even standardised within a brand. The wide variety of cell developments can therefore only be used sensibly with the help of their exact formula-tion. But there are also individual cell components, such as the cathode material or the housing of a round cell, which could be reprocessed or reused without separation, if disassembly was mechanically possible.
The third R: Recycle
The guiding principle “Recycle” comes into action when the components of a battery system cannot be reused in the sense of the second R. The aim is easy recyclability. The recycling effort is already partly determined by the sustaina-bility concept at cell level. For example, the recovery of nickel, cobalt or copper is economically worthwhile, but en-ergy intensive. Same if nickel plated steel is used, which has to be melted down in order to separate nickel and steel again. The question of how to achieve the highest possible proportion of recyclable materials should not only accom-pany the entire development and production chain of battery systems in terms of sustainability. In essence, it is also a question of balancing profit and purpose. Technically, the implementation and optimisation of sustainable battery systems are possible. Partly and increasingly, it is becoming an economic imperative, because materials that are only available in limited quantities will have to be brought back into the cycle. If it is possible to link commercial decision-making criteria more closely to the idea of sustainability, this will automatically lead to a better balance. But for this effect, responsibilities would have to shift. If the pressure to take back products can be shifted from the end of the chain to the beginning, innovation will automatically emerge. If, in the sense of polluter-pays-principle the product responsible shares the costs of recycling of his product, he will find new and better ways of designing more sustaina-ble battery systems. If he developed a business case from this, we have got a win-win situation for everyone. And when the first life cycle of batteries is completed in about ten years, an industry should already have emerged from it, with technologies and processes that are currently being developed and are ready to be applied. It is now high time to establish a stable circular economy for batteries.
Read here a concrete application of the “three Rs” to a sustainably designed battery system using the example of the modular battery system EASy Marine®: 3R: Battery recycling in the maritime industry (https://eas-batter-ies.com/news/3r-battery-recycling-maritime-industry)
Author: Dr. Frank Diehl, EAS Batteries Head of Sales and Marketing